Identify welding machine conditions
using AI
Below is a free classifier to identify welding machine conditions. Just upload your image, and our AI will predict the condition of the welding machine - in just seconds.
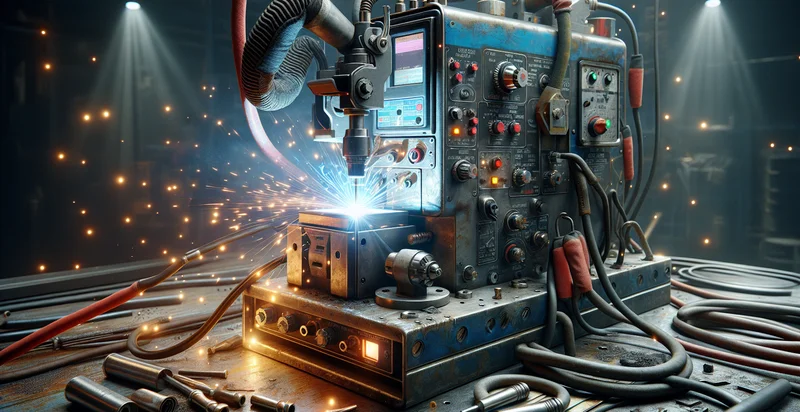
Contact us for API access
Or, use Nyckel to build highly-accurate custom classifiers in just minutes. No PhD required.
Get started
import nyckel
credentials = nyckel.Credentials("YOUR_CLIENT_ID", "YOUR_CLIENT_SECRET")
nyckel.invoke("welding-machine-conditions", "your_image_url", credentials)
fetch('https://www.nyckel.com/v1/functions/welding-machine-conditions/invoke', {
method: 'POST',
headers: {
'Authorization': 'Bearer ' + 'YOUR_BEARER_TOKEN',
'Content-Type': 'application/json',
},
body: JSON.stringify(
{"data": "your_image_url"}
)
})
.then(response => response.json())
.then(data => console.log(data));
curl -X POST \
-H "Content-Type: application/json" \
-H "Authorization: Bearer YOUR_BEARER_TOKEN" \
-d '{"data": "your_image_url"}' \
https://www.nyckel.com/v1/functions/welding-machine-conditions/invoke
How this classifier works
To start, upload your image. Our AI tool will then predict the condition of the welding machine.
This pretrained image model uses a Nyckel-created dataset and has 5 labels, including Excellent Condition, Fair Condition, Good Condition, Poor Condition and Very Poor Condition.
We'll also show a confidence score (the higher the number, the more confident the AI model is around the condition of the welding machine).
Whether you're just curious or building welding machine conditions detection into your application, we hope our classifier proves helpful.
Related Classifiers
Need to identify welding machine conditions at scale?
Get API or Zapier access to this classifier for free. It's perfect for:
- Predictive Maintenance: This function can be used to monitor welding machines in real-time, identifying any deviations from normal operating conditions. By analyzing this data, maintenance teams can predict potential failures, reducing downtime and saving costs associated with unexpected repairs.
- Quality Assurance: The false image classification function can help in ensuring that welds meet quality standards by analyzing images captured during the welding process. It can flag non-compliant welds, enabling quality control teams to address issues before they affect the final product.
- Training and Safety: By using this function in training programs, new operators can better understand acceptable welding conditions. The system can classify images of proper and improper welding practices, helping trainees learn to identify faulty techniques and improve safety protocols.
- Process Optimization: The function can assist in optimizing welding parameters by analyzing conditions under which machines operate most efficiently. Insights derived from image classification can lead to adjustments in speed, heat, and material usage, resulting in higher productivity and lower operational costs.
- Remote Monitoring: Businesses can leverage this function for remote monitoring of welding operations across multiple locations. By classifying images of welding machine conditions, supervisors can receive alerts about potential issues, allowing them to address problems proactively and ensure consistent quality across sites.
- Compliance Reporting: The false image classification function can aid in generating compliance reports for regulatory audits by ensuring that welding operations meet industry standards. By documenting machine conditions through classified images, businesses can provide concrete evidence of adherence to required specifications.
- Cost Analysis: Companies can use this function to analyze the costs associated with machine performance and part failures linked to abnormal welding conditions. By identifying patterns and correlating them with maintenance costs, businesses can make data-driven decisions to optimize their expenditure on equipment upkeep.