Identify robotic arm conditions
using AI
Below is a free classifier to identify robotic arm conditions. Just upload your image, and our AI will predict the appropriate conditions for operating a robotic arm - in just seconds.
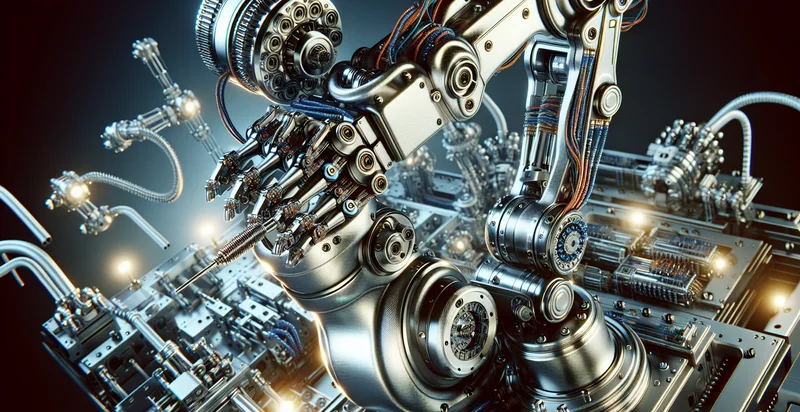
Contact us for API access
Or, use Nyckel to build highly-accurate custom classifiers in just minutes. No PhD required.
Get started
import nyckel
credentials = nyckel.Credentials("YOUR_CLIENT_ID", "YOUR_CLIENT_SECRET")
nyckel.invoke("robotic-arm-conditions", "your_image_url", credentials)
fetch('https://www.nyckel.com/v1/functions/robotic-arm-conditions/invoke', {
method: 'POST',
headers: {
'Authorization': 'Bearer ' + 'YOUR_BEARER_TOKEN',
'Content-Type': 'application/json',
},
body: JSON.stringify(
{"data": "your_image_url"}
)
})
.then(response => response.json())
.then(data => console.log(data));
curl -X POST \
-H "Content-Type: application/json" \
-H "Authorization: Bearer YOUR_BEARER_TOKEN" \
-d '{"data": "your_image_url"}' \
https://www.nyckel.com/v1/functions/robotic-arm-conditions/invoke
How this classifier works
To start, upload your image. Our AI tool will then predict the appropriate conditions for operating a robotic arm.
This pretrained image model uses a Nyckel-created dataset and has 7 labels, including Excellent Condition, Fair Condition, Good Condition, Like New Condition, Poor Condition, Very Good Condition and Very Poor Condition.
We'll also show a confidence score (the higher the number, the more confident the AI model is around the appropriate conditions for operating a robotic arm).
Whether you're just curious or building robotic arm conditions detection into your application, we hope our classifier proves helpful.
Related Classifiers
Need to identify robotic arm conditions at scale?
Get API or Zapier access to this classifier for free. It's perfect for:
- Quality Assurance in Manufacturing: This function can be employed in manufacturing settings to verify the correct assembly of robotic arms by identifying faulty components or incorrect configurations. By automating this inspection process, companies can reduce errors, improve product quality, and minimize production downtimes.
- Predictive Maintenance: Implementing the false image classification function on robotic arms can help identify conditions indicative of potential failures or malfunctions. By analyzing real-time data, maintenance teams can proactively address issues before they escalate, thus reducing costs and increasing operational efficiency.
- Automated Inspection Systems: The function can be integrated into automated visual inspection systems that assess the condition of robotic arms in various environments. By ensuring that robotic arms meet predefined standards, organizations can enhance safety and operational reliability.
- Training and Simulation: The false image classification function can be utilized in training environments for robotics and automation specialists. By providing feedback on the condition of robotic arms in simulation scenarios, learners can develop a deeper understanding of robotics maintenance and troubleshooting.
- Remote Monitoring: Businesses can employ this function in remote monitoring systems to continuously assess the condition of robotic arms deployed in inaccessible locations. This allows technicians to receive alerts about potential issues, ensuring timely interventions and reducing the need for on-site inspections.
- Production Line Optimization: The function can be used to track and identify conditions of robotic arms during production processes, allowing for data-driven decisions regarding workflow adjustments. This aids in optimizing the production line, leading to increased throughput and reduced cycle times.
- Compliance and Reporting: Organizations can leverage the function to ensure that their robotic arms comply with industry standards and regulations by regularly classifying their operational conditions. This not only facilitates easier compliance reporting but also enhances operational accountability and transparency within the organization.