Identify packaging line conditions
using AI
Below is a free classifier to identify packaging line conditions. Just upload your image, and our AI will predict the optimal packaging conditions for each product type - in just seconds.
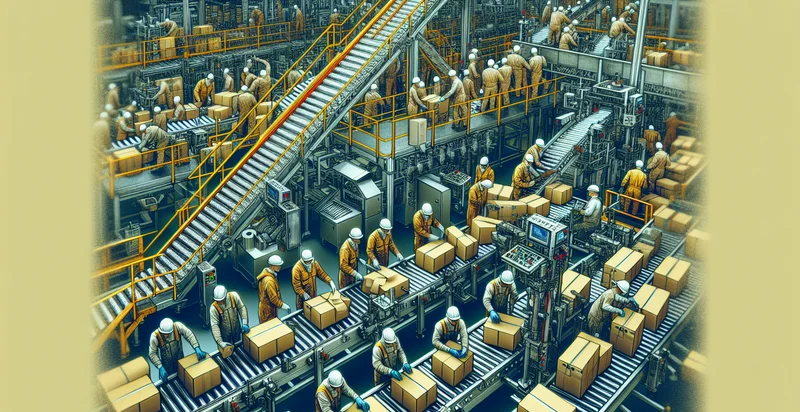
Contact us for API access
Or, use Nyckel to build highly-accurate custom classifiers in just minutes. No PhD required.
Get started
import nyckel
credentials = nyckel.Credentials("YOUR_CLIENT_ID", "YOUR_CLIENT_SECRET")
nyckel.invoke("packaging-line-conditions", "your_image_url", credentials)
fetch('https://www.nyckel.com/v1/functions/packaging-line-conditions/invoke', {
method: 'POST',
headers: {
'Authorization': 'Bearer ' + 'YOUR_BEARER_TOKEN',
'Content-Type': 'application/json',
},
body: JSON.stringify(
{"data": "your_image_url"}
)
})
.then(response => response.json())
.then(data => console.log(data));
curl -X POST \
-H "Content-Type: application/json" \
-H "Authorization: Bearer YOUR_BEARER_TOKEN" \
-d '{"data": "your_image_url"}' \
https://www.nyckel.com/v1/functions/packaging-line-conditions/invoke
How this classifier works
To start, upload your image. Our AI tool will then predict the optimal packaging conditions for each product type.
This pretrained image model uses a Nyckel-created dataset and has 31 labels, including Aligned Packaging, Clean Packaging, Completely Filled, Damaged Packaging, Dirt Present, Discoloration, Excellent Condition, Expired Packaging, Fair Condition and Fresh Packaging.
We'll also show a confidence score (the higher the number, the more confident the AI model is around the optimal packaging conditions for each product type).
Whether you're just curious or building packaging line conditions detection into your application, we hope our classifier proves helpful.
Related Classifiers
Need to identify packaging line conditions at scale?
Get API or Zapier access to this classifier for free. It's perfect for:
- Quality Control Monitoring: This function can be employed to automatically monitor the packaging line for any false images that may indicate defects or inconsistencies in product packaging. By identifying such issues in real-time, manufacturers can mitigate quality control risks and minimize waste.
- Anomaly Detection: The false image classification function can be integrated into existing surveillance systems on the packaging line to detect anomalies. This would enable prompt investigation of unexpected deviations from standard visual packaging patterns, helping to maintain operational efficiency.
- Predictive Maintenance: Leveraging false image detection can help predict failures in packaging machinery by identifying abnormal visual signals. By analyzing these signals over time, businesses can schedule proactive maintenance, thereby reducing downtime and maintenance costs.
- Training and Development: The insights generated by false image classifications can be used to design training programs for packaging line operators. Understanding what constitutes a false image can enhance staff awareness and improve their ability to respond to packaging line issues effectively.
- Compliance and Regulatory Reporting: Businesses can utilize false image classification to ensure compliance with industry standards by regularly auditing packaging processes. This system can generate reports that document compliance with visual standards, ensuring accountability and transparency during audits.
- Supply Chain Optimization: By implementing false image detection, companies can improve inventory management processes by using visual data to adjust order quantities based on detected packaging anomalies. This can optimize the supply chain by reducing overproduction and stock-outs related to damaged goods.
- Customer Satisfaction Enhancement: The implementation of this function can help ensure that only properly packaged products reach consumers, thereby reducing complaints related to packaging defects. Enhanced packaging integrity translates to higher customer satisfaction and brand loyalty.