Identify hydraulic press conditions
using AI
Below is a free classifier to identify hydraulic press conditions. Just upload your image, and our AI will predict the optimal conditions for using a hydraulic press - in just seconds.
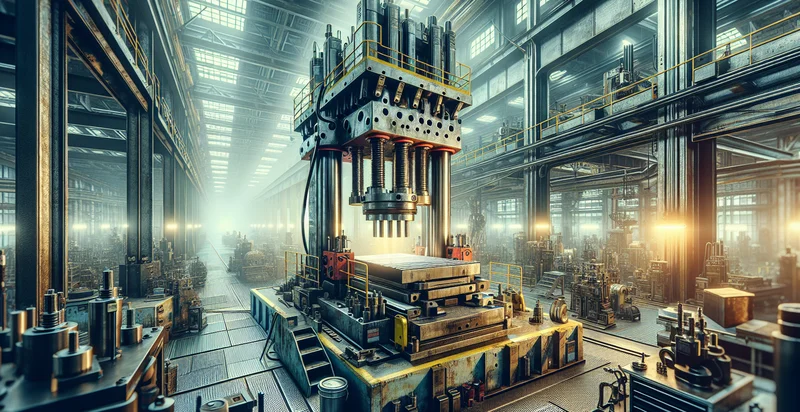
Contact us for API access
Or, use Nyckel to build highly-accurate custom classifiers in just minutes. No PhD required.
Get started
import nyckel
credentials = nyckel.Credentials("YOUR_CLIENT_ID", "YOUR_CLIENT_SECRET")
nyckel.invoke("hydraulic-press-conditions", "your_image_url", credentials)
fetch('https://www.nyckel.com/v1/functions/hydraulic-press-conditions/invoke', {
method: 'POST',
headers: {
'Authorization': 'Bearer ' + 'YOUR_BEARER_TOKEN',
'Content-Type': 'application/json',
},
body: JSON.stringify(
{"data": "your_image_url"}
)
})
.then(response => response.json())
.then(data => console.log(data));
curl -X POST \
-H "Content-Type: application/json" \
-H "Authorization: Bearer YOUR_BEARER_TOKEN" \
-d '{"data": "your_image_url"}' \
https://www.nyckel.com/v1/functions/hydraulic-press-conditions/invoke
How this classifier works
To start, upload your image. Our AI tool will then predict the optimal conditions for using a hydraulic press.
This pretrained image model uses a Nyckel-created dataset and has 10 labels, including As New Condition, Excellent Condition, Expired Condition, Fair Condition, Good Condition, Needs Maintenance, Operational Condition, Poor Condition, Serviceable Condition and Undergoing Repairs.
We'll also show a confidence score (the higher the number, the more confident the AI model is around the optimal conditions for using a hydraulic press).
Whether you're just curious or building hydraulic press conditions detection into your application, we hope our classifier proves helpful.
Related Classifiers
Need to identify hydraulic press conditions at scale?
Get API or Zapier access to this classifier for free. It's perfect for:
- Quality Control in Manufacturing: The hydraulic press conditions identifier can be integrated into manufacturing processes to monitor and ensure optimal conditions during metal forming operations. By identifying false images related to incorrect pressure application, manufacturers can reduce defects and maintain high product quality.
- Predictive Maintenance: This function can be leveraged to analyze the operational conditions of hydraulic presses, predicting potential failures before they occur. By analyzing image data, businesses can schedule maintenance more effectively, minimizing downtime and repair costs associated with equipment failure.
- Safety Compliance Monitoring: Companies can use the identifier to ensure that hydraulic presses operate within regulated safety conditions. By automatically detecting unsafe operational states or anomalies, businesses can enhance workplace safety and ensure compliance with industry regulations.
- Training and Simulation: The identifier can be employed in training programs for operators of hydraulic presses. By providing simulated scenarios and identifying false images, trainees can learn to recognize and react to improper conditions, improving their skills and safety awareness.
- Process Optimization: By analyzing the conditions under which hydraulic presses operate effectively, businesses can optimize their processes for maximum efficiency. The identifier can help identify patterns in false image occurrences, enabling companies to fine-tune operational parameters for better throughput and energy usage.
- Fault Diagnosis and Resolution: This function can assist in diagnosing faults within hydraulic systems by identifying and categorizing false images. The quick identification of discrepancies allows technicians to resolve issues swiftly, reducing repair times and enhancing overall system reliability.
- Remote Monitoring Solutions: The hydraulic press conditions identifier can be incorporated into IoT-enabled systems for remote monitoring of hydraulic presses. This capability allows managers to receive real-time alerts about operational conditions, enabling quick decision-making and intervention without needing to be physically present on-site.