Identify drill press conditions
using AI
Below is a free classifier to identify drill press conditions. Just upload your image, and our AI will predict the optimal settings for operating a drill press under various conditions. - in just seconds.
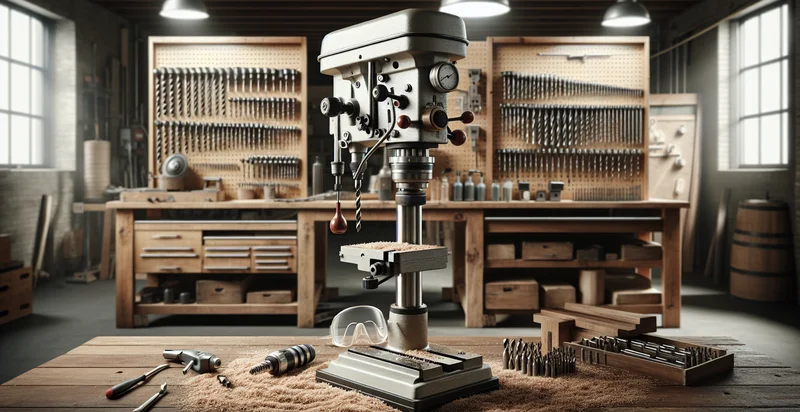
Contact us for API access
Or, use Nyckel to build highly-accurate custom classifiers in just minutes. No PhD required.
Get started
import nyckel
credentials = nyckel.Credentials("YOUR_CLIENT_ID", "YOUR_CLIENT_SECRET")
nyckel.invoke("drill-press-conditions", "your_image_url", credentials)
fetch('https://www.nyckel.com/v1/functions/drill-press-conditions/invoke', {
method: 'POST',
headers: {
'Authorization': 'Bearer ' + 'YOUR_BEARER_TOKEN',
'Content-Type': 'application/json',
},
body: JSON.stringify(
{"data": "your_image_url"}
)
})
.then(response => response.json())
.then(data => console.log(data));
curl -X POST \
-H "Content-Type: application/json" \
-H "Authorization: Bearer YOUR_BEARER_TOKEN" \
-d '{"data": "your_image_url"}' \
https://www.nyckel.com/v1/functions/drill-press-conditions/invoke
How this classifier works
To start, upload your image. Our AI tool will then predict the optimal settings for operating a drill press under various conditions..
This pretrained image model uses a Nyckel-created dataset and has 4 labels, including Excellent Condition, Fair Condition, Good Condition and Poor Condition.
We'll also show a confidence score (the higher the number, the more confident the AI model is around the optimal settings for operating a drill press under various conditions.).
Whether you're just curious or building drill press conditions detection into your application, we hope our classifier proves helpful.
Related Classifiers
Need to identify drill press conditions at scale?
Get API or Zapier access to this classifier for free. It's perfect for:
- Equipment Maintenance Alerts: This function can be used to monitor drill press conditions and identify when anomalies occur, signaling that maintenance is required. By proactively addressing these issues, businesses can reduce downtime and extend the life of their equipment.
- Quality Control Enhancement: The false image classification function can help in assessing the quality of parts produced by a drill press. By identifying defects early, manufacturers can ensure higher product quality and reduce waste from flawed parts.
- Operator Training Programs: The technology can be integrated into training modules for new operators. By simulating conditions and identifying false images, employees can learn to recognize and address problematic scenarios before they occur in real production environments.
- Process Optimization: Companies can analyze the data generated from false image classifications to optimize drilling conditions. This analysis can lead to improved efficiency, cost reduction, and a better understanding of operational parameters.
- Safety Monitoring: The function can serve as a safety guard by identifying potential hazards associated with drill press operation. By flagging unsafe conditions, operators can avoid accidents and enhance workplace safety.
- Performance Benchmarking: Organizations can use the function to compare operational performance against industry standards. By analyzing the classification results, businesses can identify areas for improvement and implement best practices effectively.
- Predictive Analytics Integration: Incorporating the false image classification function into a predictive analytics framework allows businesses to anticipate equipment failures. This foresight can lead to more informed decision-making and improved inventory management for spare parts.