Identify distillation unit conditions
using AI
Below is a free classifier to identify distillation unit conditions. Just upload your image, and our AI will predict the optimal operating conditions for a distillation unit. - in just seconds.
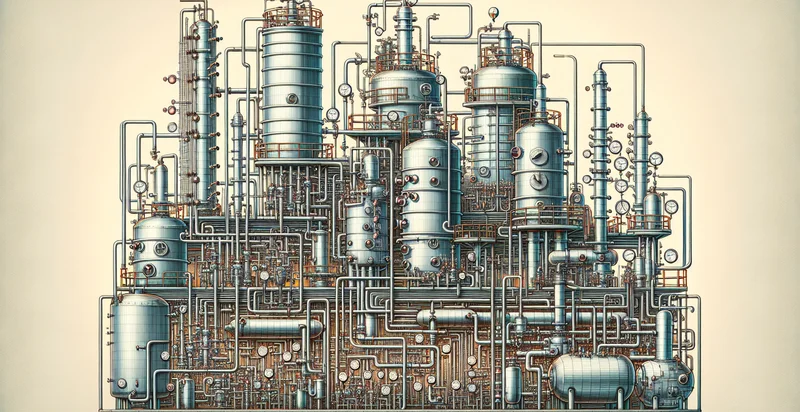
Contact us for API access
Or, use Nyckel to build highly-accurate custom classifiers in just minutes. No PhD required.
Get started
import nyckel
credentials = nyckel.Credentials("YOUR_CLIENT_ID", "YOUR_CLIENT_SECRET")
nyckel.invoke("distillation-unit-conditions", "your_image_url", credentials)
fetch('https://www.nyckel.com/v1/functions/distillation-unit-conditions/invoke', {
method: 'POST',
headers: {
'Authorization': 'Bearer ' + 'YOUR_BEARER_TOKEN',
'Content-Type': 'application/json',
},
body: JSON.stringify(
{"data": "your_image_url"}
)
})
.then(response => response.json())
.then(data => console.log(data));
curl -X POST \
-H "Content-Type: application/json" \
-H "Authorization: Bearer YOUR_BEARER_TOKEN" \
-d '{"data": "your_image_url"}' \
https://www.nyckel.com/v1/functions/distillation-unit-conditions/invoke
How this classifier works
To start, upload your image. Our AI tool will then predict the optimal operating conditions for a distillation unit..
This pretrained image model uses a Nyckel-created dataset and has 6 labels, including Excellent Condition, Fair Condition, Good Condition, Poor Condition, Very Good Condition and Very Poor Condition.
We'll also show a confidence score (the higher the number, the more confident the AI model is around the optimal operating conditions for a distillation unit.).
Whether you're just curious or building distillation unit conditions detection into your application, we hope our classifier proves helpful.
Related Classifiers
Need to identify distillation unit conditions at scale?
Get API or Zapier access to this classifier for free. It's perfect for:
- Condition Monitoring: This function can be employed to continuously monitor the operating conditions of the distillation unit in real time. By identifying false images or anomalies in data, it enables timely interventions, reducing the risk of equipment failures and optimizing operational efficiency.
- Quality Control: By integrating the identifier into quality control processes, manufacturers can ensure that only compliant conditions are sustained during distillation. This leads to improved product quality while reducing wastage of materials due to improperly processed batches.
- Predictive Maintenance: The identifier can predict maintenance needs by analyzing changes in the true operating conditions of the distillation unit. This proactive approach minimizes unplanned downtime by allowing maintenance teams to address issues before they escalate.
- Fault Diagnosis: In the event of a deviation from normal distillation conditions, the function aids engineers in diagnosing the underlying causes. This can expedite problem resolution, preventing extended disruptions in production.
- Safety Compliance: The function can help ensure that the distillation unit operates within regulatory safety limits. By identifying false images in process data, it aids in maintaining adherence to safety standards, thus protecting personnel and reducing liability risks.
- Energy Management: By analyzing the conditions of the distillation unit, the function can highlight areas for energy savings. This can lead to more sustainable operations and lower operational costs through optimized energy consumption.
- Training and Simulation: The identifier can be used in training programs to simulate various operating conditions within the distillation unit. This aids in developing the skills of technicians and operators, ensuring they can effectively respond to anomalies in real scenarios.