Identify bearing system conditions
using AI
Below is a free classifier to identify bearing system conditions. Just upload your image, and our AI will predict the condition of the bearing system components - in just seconds.
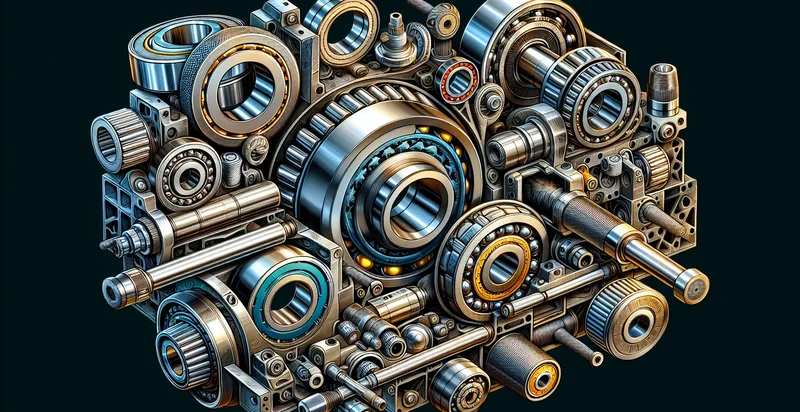
Contact us for API access
Or, use Nyckel to build highly-accurate custom classifiers in just minutes. No PhD required.
Get started
import nyckel
credentials = nyckel.Credentials("YOUR_CLIENT_ID", "YOUR_CLIENT_SECRET")
nyckel.invoke("bearing-system-conditions", "your_image_url", credentials)
fetch('https://www.nyckel.com/v1/functions/bearing-system-conditions/invoke', {
method: 'POST',
headers: {
'Authorization': 'Bearer ' + 'YOUR_BEARER_TOKEN',
'Content-Type': 'application/json',
},
body: JSON.stringify(
{"data": "your_image_url"}
)
})
.then(response => response.json())
.then(data => console.log(data));
curl -X POST \
-H "Content-Type: application/json" \
-H "Authorization: Bearer YOUR_BEARER_TOKEN" \
-d '{"data": "your_image_url"}' \
https://www.nyckel.com/v1/functions/bearing-system-conditions/invoke
How this classifier works
To start, upload your image. Our AI tool will then predict the condition of the bearing system components.
This pretrained image model uses a Nyckel-created dataset and has 10 labels, including Acceptable Condition, Critical Condition, Excellent Condition, Fair Condition, Good Condition, Moderate Condition, Optimal Condition, Poor Condition, Satisfactory Condition and Very Poor Condition.
We'll also show a confidence score (the higher the number, the more confident the AI model is around the condition of the bearing system components).
Whether you're just curious or building bearing system conditions detection into your application, we hope our classifier proves helpful.
Related Classifiers
Need to identify bearing system conditions at scale?
Get API or Zapier access to this classifier for free. It's perfect for:
- Predictive Maintenance: By utilizing the false image classification function, businesses can analyze images of bearing systems to identify potential failures before they occur. This proactive approach reduces downtime and extends equipment lifespan, leading to significant cost savings in maintenance.
- Quality Control in Manufacturing: Manufacturers can leverage the bearing system conditions identifier to monitor the quality of bearing components in production. By classifying images accurately, defects can be detected early, ensuring only high-quality products reach the market.
- Remote Monitoring Systems: Companies can integrate the image classification tool into their remote monitoring solutions for bearing systems. This allows for constant surveillance of critical infrastructure, enabling quick responses to emerging issues without the need for physical inspections.
- Training and Development: The classification function can serve as a valuable tool for training employees in recognizing bearing system conditions through image analysis. By improving knowledge and awareness, organizations can enhance their workforce’s expertise in maintenance tasks.
- Integration with IoT Devices: The bearing condition identifier can be integrated into IoT-enabled machinery, allowing for real-time image analysis and classification of bearing conditions. This integration enhances decision-making capabilities on the shop floor and streamlines processes through automated alerts.
- Research and Development: R&D teams can utilize the false image classification function to analyze experimental bearing designs and their conditions under various operating scenarios. This helps expedite the design process, resulting in the creation of more reliable and efficient bearing systems.
- Customer Support and Reporting: Organizations can employ the image classification tool to assess and report on customer complaints regarding bearing system performance. By providing accurate analysis and documentation, support teams can offer more effective solutions and improve customer satisfaction.